Extruder Duty Helical Gearboxes Are the Heart of Modern Food Machinery
The food processing industry weights strong, consistent, and hygienic machinery capable of operating continuously under demanding conditions. At the fundamental of many extrusion processes – from, bakery products, dairy products, pasta and pet food manufacturing to the production of snacks and confectionery – lies the extruder, a powerful machine driven by an expert gearbox: the extruder duty helical gearbox.
These type of gearboxes are engineered to withstand the extreme pressures, torques, and potentially abrasive materials inherent in extrusion, playing a critical role in ensuring efficient and safe production. Well, Gamma Gears is world’s one of the best worm reduction gearbox manufacturing company in Ahmedabad, Gujarat, India.
Accepting today’s Scenario about Demands of Extrusion:
Extrusion machinery mechanism processes involve forcing a material – a dough, paste, or other semi-solid substance – through a die to create a specific shape. This process generates significant torque and pressure, specifically when dealing with viscous materials or high throughput rates.
The extruder duty helical gearbox with universal mounting type gearbox could be the most capable of handling these forces without compromising performance or operational lifespan. Food safety regulations also demand stringent hygiene standards, requiring gearboxes constructed from materials that are easy to clean, corrosion-resistant, and free from potential pollutants.
The Role of the Extruder Duty Helical Gearbox:
Helical gearboxes are preferably suited for extruder machinery mechanism applications due to their inherent advantages over other gearbox types:
High Torque Capacity: The helical gear design, with its angled teeth, allows for smoother power transmission and increased torque capacity compared to spur gears. This is crucial for overcoming the resistance encountered during extrusion. The smooth engagement of helical teeth also reduces noise and vibration, backing to a well-organized and noiseless operation.
High Efficiency: The smooth meshing of helical gears minimizes friction losses, resulting in higher efficiency compared to other gear types. This translates to reduced energy consumption and lower operating costs, a significant factor in the cost-sensitive food processing industry.
Compact Design: Notwithstanding their high torque capacity, helical gearboxes can often be more compact than other gearbox types, making them suitable for integration into space-constrained processing lines.
Robustness and Endurance: Constructed from high-strength materials such as hardened steel, these gearboxes are built to withstand the continuous heavy-duty operation characteristic of extrusion. Accurate manufacturing techniques ensure accurate tooth alignment and minimal wear, contributing to a long service life.
Specialized Features for Food Machinery Applications:
Extruder duty helical gearboxes used in food processing often incorporate several specialized features to meet the unique demands of the industry:
Food-Grade Materials: The gearboxes are characteristically constructed from stainless steel or other corrosion-resistant materials that can survive frequent cleaning and sanitization procedures. This ensures the absence of material degradation and prevents uncleanness of the processed food.
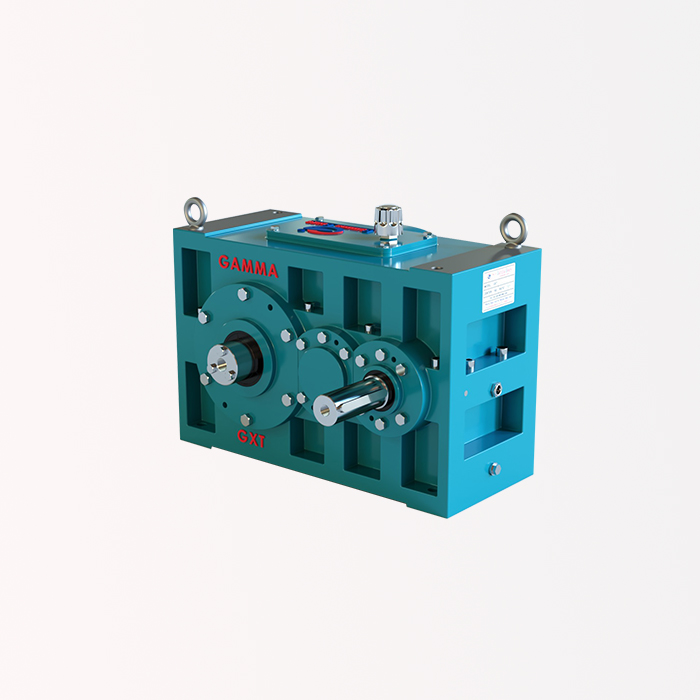
Closed Housings: The gearboxes are designed with sealed housings to protect internal components from dust, moisture, and other environmental contaminants. This minimizes the risk of damage and maintains hygiene standards.
Laid-back Clean Ability: The external design is optimized for easy cleaning and maintenance. Smooth surfaces and absence of crevices minimize the potential for bacterial growth. The use of willingly cleanable seals and gaskets further enhances hygiene.
Lubrication Systems: Proficient lubrication systems are vital for maintaining the gearbox’s long-term performance and reducing wear. Food-grade lubricants are used to ensure compliance with safety regulations.
Value-added Optional Features: Other technical features, such as thermal overload protection and integrated sensors for monitoring operating parameters, further enhance the safety and reliability of these gearboxes.
Decide on the appropriate extruder duty helical gearbox requires careful consideration of several factors are appropriate torque requirements, speed ratio with respective calculation, mounting configuration, environmental conditions at manufacturing, minimal maintenance requirements. Contact to Gamma Gears is world’s one of the best worm reduction gearbox manufacturing company in Ahmedabad, Gujarat, India.